The American statesman Ben Franklin is credited with saying that a successful organization requires “a place for everything and everything in its place.” Or, as ITER Facility Management Officer Guillaume Roux puts it, “you don’t want to put a cat in a room built for an elephant.”
The quest to maximize the use of space on the ITER site has been a preoccupation since building began in 2010—both on the 42-hectare platform that houses the ITER research infrastructure and in the surrounding office, storage, and contractor zones.
“Even if the site seems big, there isn’t enough space,” explains Roux, who’s been with ITER’s Construction Management Office (CMO) since 2019. “As the construction needs evolve, you have to create use-of-space scenarios for the buildings with different risks and costs so you can foresee every possible situation and make sure everything fits together properly.”
A recent example arose when the square footage dedicated to the temporary vacuum laboratory in the basement of ITER Headquarters was needed for ITER’s data centre. A new vacuum lab was required and, ideally, it would offer even more space so that larger components, such as the huge seals for the vacuum vessel port plugs, could be tested.
We’ve needed to consolidate space used across the ITER and CEA sites into one proper lab for a while,” says Robert Pearce, the Vacuum Delivery & Installation Section Leader. “It’s essential for confirming components are correct in design and construction before entering the tokamak.”
The project began to take shape under Roux’s guidance in 2020. After the lab’s technical specifications were established with upgrades—such as a 20-tonne interior crane instead of the old 1-tonne crane—it became a question of location. One space-saving option was to put the lab outside ITER, but this added logistical obstacles. Another was to try and squeeze the lab into an existing building on the main ITER platform, but these structures are in high demand and thus every square metre is incredibly valuable. ITER leaders opted for a new facility, Building 99, and found a location in a new contractors area under development at the northwestern edge of the platform.
Because it is more efficient to have multiple laboratories in a single building, a search was launched for a partner to share the space and budget. A fitting candidate was soon identified: the Tritium Plant Section, which would need a facility to test prototype and first-production units using hydrogen and deuterium, such as the hydride beds that will be used to safely and passively store fuel for the plasma.
“Our need wasn’t as pressing but my vision is holistic,” says Ian Bonnett, the Tritium Plant Section Leader. “A workshop was required to support vacuum systems before First Plasma, so we joined the project and will add tritium plant equipment progressively as we move forward.”
With the partners in place, a budget was approved for a building with 740m² of floor space for major testing and a 140m² mezzanine for lighter testing. The tender went out in January 2021 and a consortium of French firms—CHAPUS as leader along with MCM, FCIE, and Actemium—began construction in May 2021. For Roux, who grew up in a family of masons and previously had his own construction company, this part was second nature.
“One of my added values is the experience I have in the building sector,” he explains. “This helps me to prepare realistic schedules and cost estimates and make sure everything is delivered on time and on budget.”
Building 99 was officially opened in January 2022 and testing of vacuum components is underway, with the first tritium equipment likely to be installed in 2023. Roux could not attend the opening ceremony due to paternity leave, but that didn’t bother him.
“I am just happy to see the equipment and the activity in the building,” says Roux with a smile. “It means my plan worked and the building was delivered on deadline.”
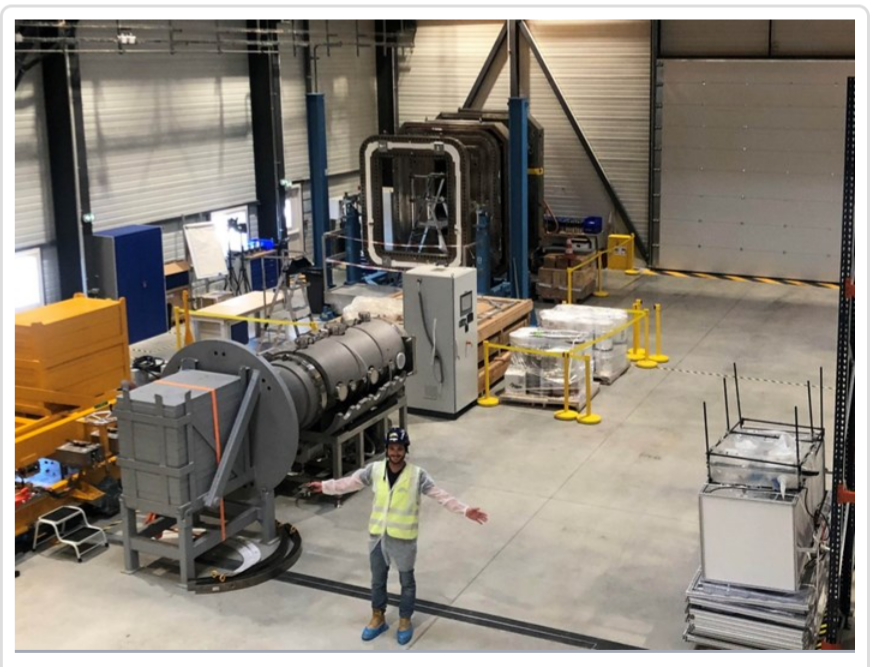
Guillaume Roux, from the ITER Construction Management Office, was involved from the project’s earliest days and saw the project through to completion.
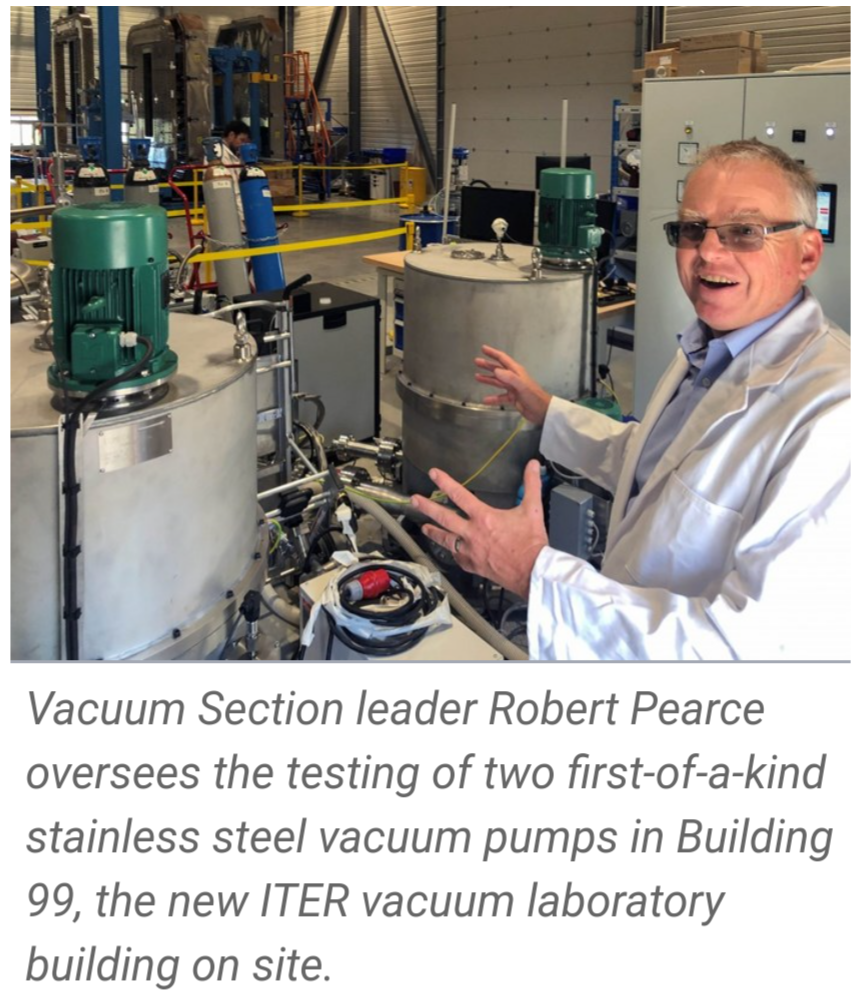
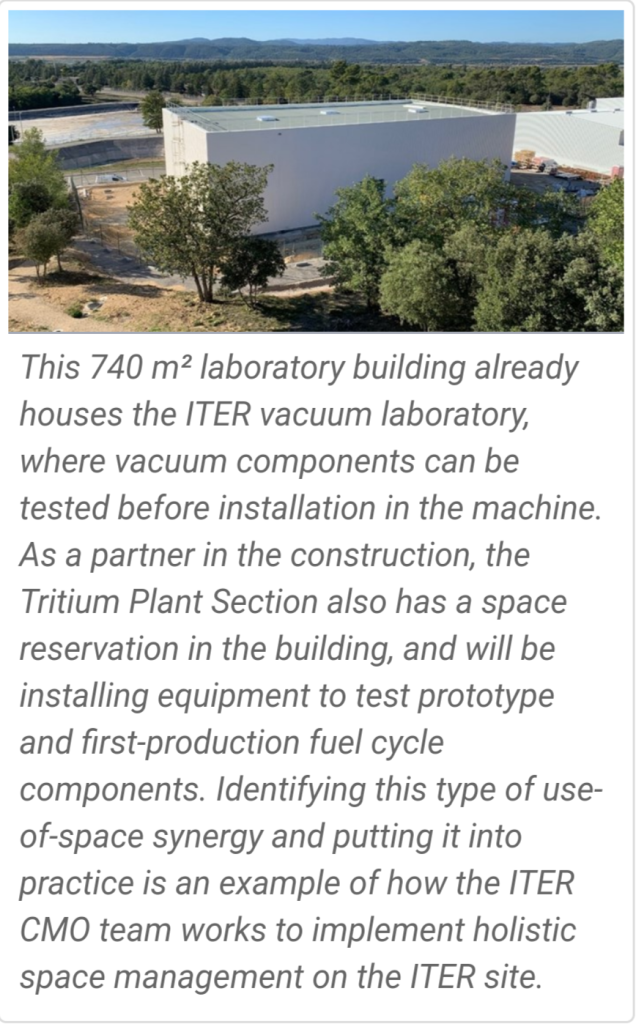