EXTRA SUPPORT FROM BELOW. Tokamak assembly.
Underneath the concrete slab that supports the Tokamak Complex is a vast, dimly lit space whose only features are squat, pillar-like structures called “plinths.” Sandwiched between the top of the pillars and the slab above, flexible seismic pads ensure that in the event of an earthquake, the integrity of the building will be protected from sudden and strong horizontal accelerations.
Out of a total of 493 plinths, 90 are arranged in a circle underneath the tokamak “crown” and the bioshield wall, which together will support the 23,000-tonne machine and absorb the brunt of the horizontal and rotational forces during operation. Only one is required directly under the centre of the machine below the central solenoid magnet. For the duration of machine assembly, however, this central point is subject to extra pressure due to the configuration of assembly tooling and requires extra support. A temporary propping system is already in place.
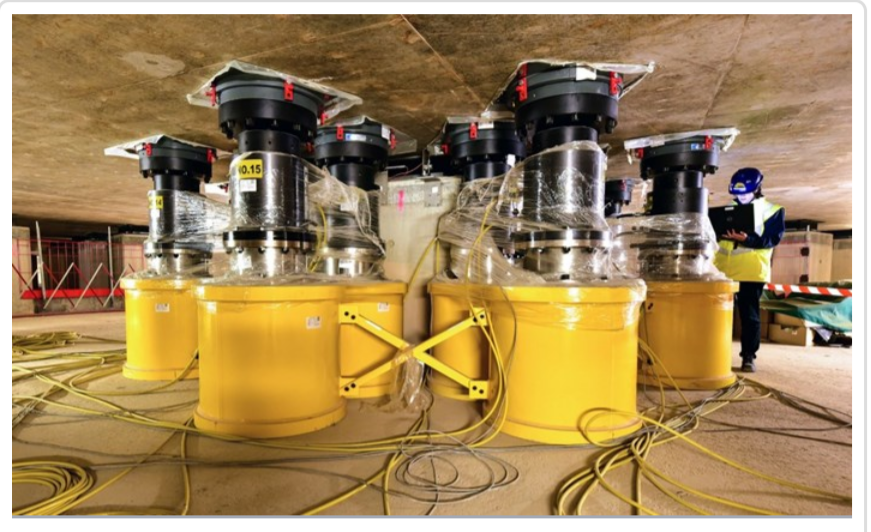
A concrete “crown” under the machine, radially anchored every 20 degrees in the bioshield, will support the combined mass of the vacuum vessel, magnets and cryostat (23,000 tonnes) and direct loads outward to the exceptionally thick and strong bioshield.
During the assembly phase, however, the distribution of mass is quite different—with the dead weight of the installed components supported by two temporary assembly tools: the central column, anchored in the concrete slab of the Tokamak Building, and the radial beams supported between the central column and the bioshield wall. In order to compensate the pressure that the central column exerts on the central seismic plinth, a temporary propping system was installed in December 2021 at the very centre of the seismic support arrangement. This passive device will stay in place until the completion of tokamak assembly activities.
Precisely positioned under the central column, below the basemat slab, 16 massive propping elements stand in a close circle around the lone central plinth.
Each of the elements comprises a powerful hydraulic jack sitting on a metal stool and equipped with a rotational head and sliding bearings. “In case of a seismic event during the assembly phase, it is essential that the propping system does not interfere with the building’s behaviour,” explains Armand Gjoklaj, a nuclear engineer in ITER Buildings & Civil Works Section. “The jacks’ rotational head and the horizontal sliding bearings’ Teflon sheets contribute to the building’s freedom of movement.”
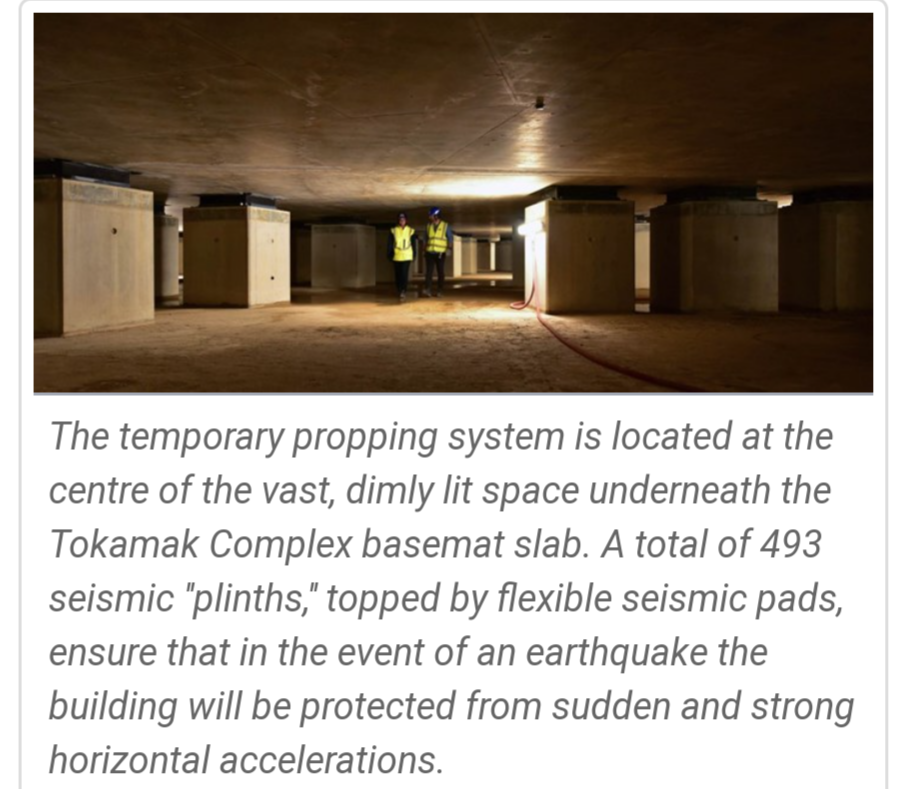
With only one sector module installed and weighing on the central column for the moment, the portion of the present load transferred to the temporary propping system is on the order of 350 tonnes—way below its nominal capacity of 8,000 tonnes. (The vertical load from the central column in case of seismic event is conservatively estimated at 5,600 tonnes.) The system capacity is defined to also limit the relative vertical displacements of the central seismic pad (on the order of one millimetre), which are monitored in real time by an array of gauges and load cells.
As more modules and other components are installed in the Tokamak assembly pit, the load transferred to the propping system will increase until installation is complete and the central column and radial beams are removed. At that time, the crown and bioshield wall will take over the heavy task of supporting the machine.